Everything you need to know about plaster and its applications
TweetWhat do you mean by plaster?
This is the procedure of plastering rough walls, rough terrain, as well as other structures with a plastic substance known as plaster or mortar.
When plaster or cement is put to the external surface of a wall to improve its look or to protect it from weather agents such as rain, heat, and so on, the term rendering is used rather than plastering.
Essentials to make a high-quality plaster
Plastering materials must meet the following requirements in order to be considered good plasters:
- During drying and setting, the volume should not decrease. This will result in cracks and an unsightly appearance.
- In all variations of climate change, it should remain adhered to the background. It should also be able to be applied regardless of the weather.
- With the required decorative effect and durability, it should be hard and durable, with an even, non-absorbent surface that can be washed.
- Cheap and economical should be the key factors.
- Surface moisture should be effectively prevented from entering or penetrating.
Varieties of Plasters
Mud Plaster
Mud plaster is made by combining equal parts well-tempered clay or brick earth with chopped straw, hay, loose soil, hemp, and cow dung.
This mixture is thoroughly mixed with a large amount of water and is lifted for about 7 days.
A mixture of clay and sand is sometimes used to make mud plaster. This mixture is mixed again thoroughly until it reaches the desired consistency.
Cement Plaster
The cement plaster is made up of one part cement and four parts clean, coarse, angular river sand by volume. The components are completely mixed in a dry state before water is added.
Materials are mixed, or a waterproof platform and plaster from one cement bag are made at a time, and this amount of plaster is consumed within 30 minutes of adding water.
Lime Plaster
It is possible to use fat lime or hydraulic lime in plastering. The best plaster is fat lime, which makes good putty when slaked.
In contrast, hydraulic lime produces a harder and stronger plaster. The plastering may form blisters, however, if some unslaked particles absorb moisture from the atmosphere and slow slake (over 8 to 12 months).
If hydraulic lime is used, it should be ground dry with sand, lifted for 2 or 3 weeks, and then reground before use.
A 4.5 kg bag of gum gal (a fragrant gum) and a 2.7 kg bag of chopped hemp are sometimes added to each 2.85 cubic meter wall plaster. In this way, cracks in the plaster are prevented from forming as it dries.
Backdrops in the Plastering Process
The Blistering and Blowing Of plaster
This comprises of tiny patches of plaster expanding out beyond the plastered surface and is caused mostly by poor slaking of lime particles in the plaster.
Following the application of plaster, the unslacked particles in the lime begin slaking, resulting in the fault. To avoid blistering, properly slaked lime should be applied.
Plaster Falling off
The reasons for the falling of plaster are as follows:
- There may be problems with the adhesion of the plaster to the background.
- It is possible that the backing material does not suction uniformly. Plaster loses its strength and mechanical bond between the two surfaces where the backing material absorbs too much water.
- It is possible that the successive plaster costs are not perfectly bonded.
- Plaster or backing that has experienced excessive thermal change.
- Plaster that has not been properly cured
Flaking in the plaster
Flaking is the emergence of a very tiny loss of mass on the plastered surface caused mostly by a bond failure between consecutive layers of plaster.
Plaster popping in place
When the plaster is set, the particles in the mix expand. In front of the particle, a conical hole is produced on the plastered surface. The blast or pop refers to this conical hole.
Stains due to rust
Sometimes seen on plastered surfaces, particularly when plaster is applied to metal lath.
Irregular Surface
It is only due to poor workmanship that this defect becomes apparent.
Weakness in the plaster
There are some areas on the plastered surface that are soft due to excessive dampness. Such softness is primarily caused by an undue thinness of the finishing coat.
Undercoat suction is excessive, deliquescent salts are present, etc.
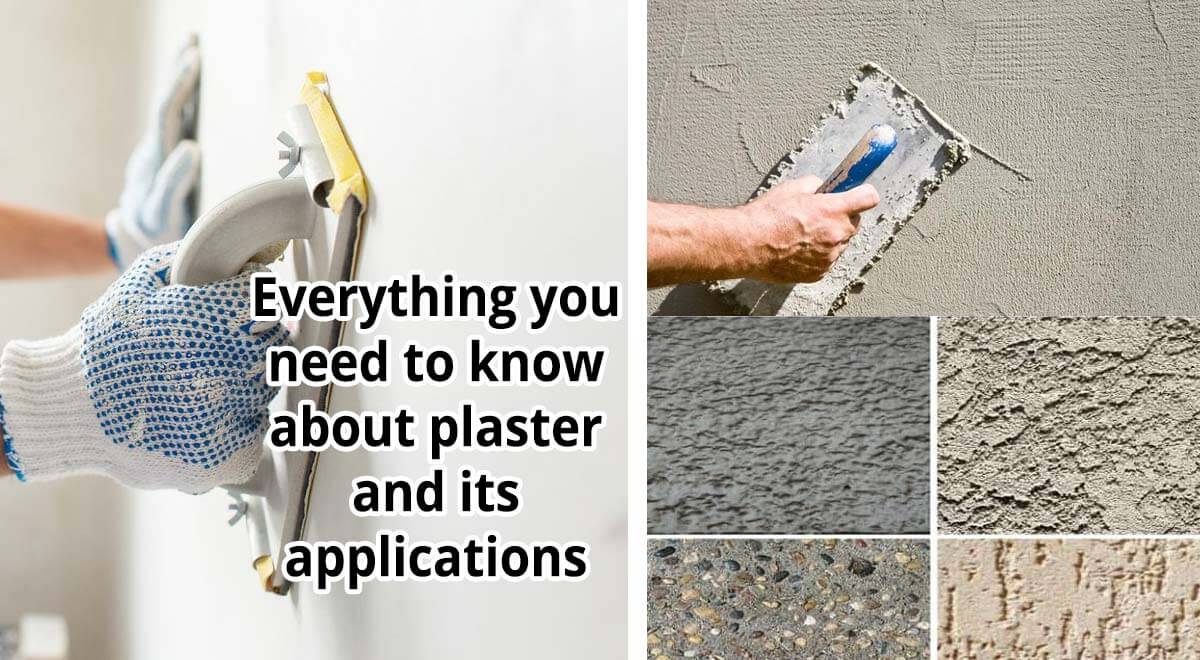