Everything you need to know about foam concrete
TweetWhat do you mean by Foam Concrete?
There are several ways to fabricate foam concrete, but the most popular way to produce foam concrete is by combining a cement paste (slurry or mortar) with a prepared foam in order to generate foam objects.
In terms of the amount of air that is entrained in foam concrete, it can be distinguished from air-entrained concrete in terms of how much air is entrained in it. It is estimated that 3 to 8 per cent of the air is absorbed in the concrete that has air entrained.
Additionally, there is another difference between aerated concrete and retarded mortar which is due to the percentage of air entrained in the concrete. A retarded mortar system is estimated to be 15 to 22 per cent more expensive than a regular mortar system. When it comes to aerated concrete, the bubbles are chemically formed as a result of the aeration process.
How is Foam Concrete Produced?
To produce foam concrete, a dilution of a surfactant in water is used, which is then passed through a foam generator, which produces a foam that is of a stable form that will last for several days. Foam is formed by mixing the cementitious mortar or grout with the foam produced so that a foamed quantity of the desired density can be produced.
A low-density fill is also manufactured using these surfactants. Controlled low-strength materials are also called CLSMs. A mix of low cement content and rich sand is added directly to foam to obtain an air content of 15 to 25 per cent. Some manufacturers supply low-density fillers as foamed concrete, so caution must be exercised. For the production of foamed concrete, there are two main methods:
- Pre-foam Method
- Inline Method
The Pre-Foam Method for Foam Concrete Production
Using this method, the base material is delivered to the site by a ready-mix truck. During rotation, the mixer injects the pre-formed foam into the truck from the other end.
It is therefore possible to produce small quantities of foam concrete for small tasks, such as grouting or trench filling. This method would produce foam concrete with a density ranging from 300 kg/m3 to 1200 kg/m3 depending on the density of the mixture. A 20 to 60 per cent air percentage will be added to the foam input to produce the foam. In order to calculate the final volume of the foam, one has to reduce the amount of other base material in order to reach the final volume. In order to carry out this procedure, a truck is used.
For this method, controlling steady air and density is challenging. It is necessary to specify and allow for a certain amount of under and over yield. The foam is mixed with a cement mortar mixture that has a water to cement ratio of 0.4 to 0.6 when it is created. The foam becomes unstable if the mortar is damp. Pre-foam is challenging to combine if the environment is too dry.
The Inline Method for Foam Concrete Production
A unit is filled with the foundational cement and sand mixture. The mix and foam are properly combined in this unit. The mixing procedure is controlled in a suitable manner. Larger volumes may be mixed easier thanks to this. The inline approach consists of two processes:
- Dry Method Inline System
- Wet Method Inline System
Dry Method Inline System: Dry materials are utilised here. They are placed inside the ship's silos. From here, they are accurately weighed and combined using on-board mixers. After that, a mixing chamber is pumped with the combined basic materials. Foam is introduced and blended while producing foam concrete in a wet manner. This technique uses a lot of water to combine the ingredients. A single supply of cement or a fly ash blend can provide 130 cubic metres of foamed concrete.
Wet Method Inline System: In comparison to the dry method, the wet method will involve the use of a wetter type of material. In order to mix these two materials together, a series of static inline mixers are used to feed and mix both the base material and the foam at the same time. On board, a continuous density monitor is used to ensure that all the ingredients are being blended together to ensure the best results.
Depending on the density of the foamed concrete, the output volume of the ready mixed truck is not the same as the output volume of the foamed concrete. Consequently, it is important to note that one 8m3 delivery of base material will produce 35m3 of foamed concrete of a density of 500kg/m3.
The looks of the Foam Cement
In a way, the foam that is manufactured to produce foam concrete is similar to shaving foam in that it is manufactured from the same chemical process. Upon mixing this with the mortar that meets the standard specifications.
The Mertis of Foam Cement
- It is easy to make foam concrete batches, so quality control and quality assurance are easy to do
- It is important to note that foam concrete structures have excellent properties for spreading and distributing loads
- It is easy to check and control the quality of foam concrete batches because they are easy to produce
- Foam concrete is more resistant to freezing and thawing than regular concrete.
- Foam Cement is budget friendly and requires very low maintenance.
The Demerits of Foam Cement
- Foam concrete is very sensitive to water in the mix because water is present in the material
- Foram Concrete have a difficulty in performing its finishing.
- When the density of the material increases, the compressive strength and the flexural strength decrease as well.
- The time required in the mixing of foam cement is extremely high.
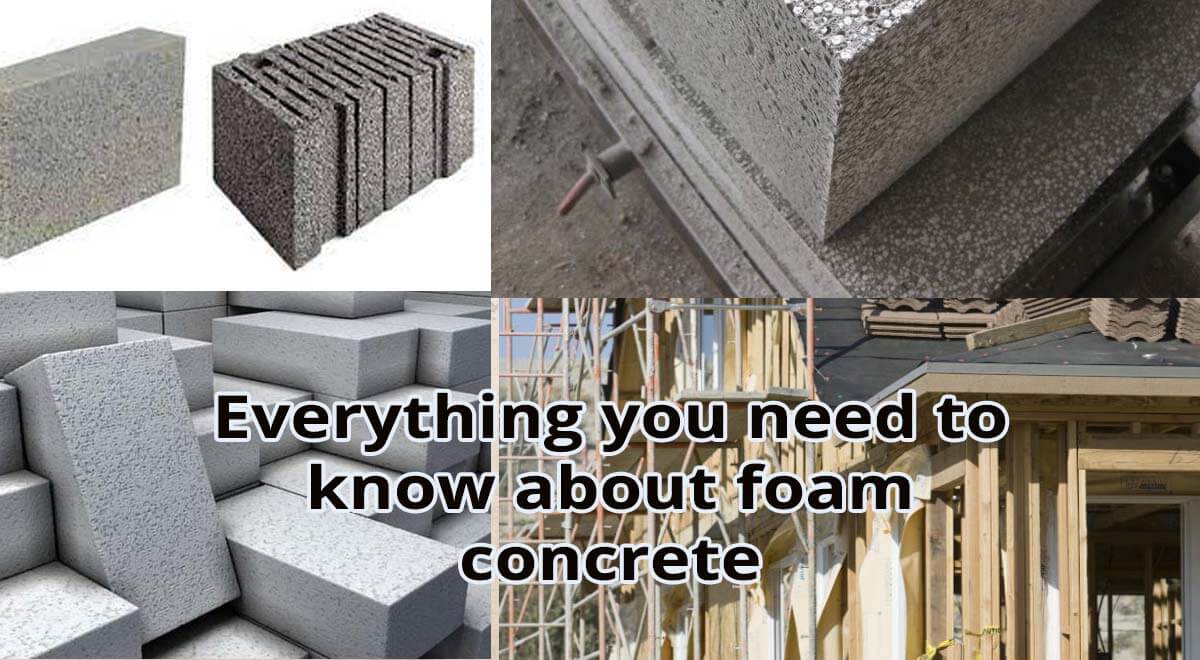